Understanding condition monitoring: A guide for engineers
This page provides a detailed overview of condition monitoring, its importance, benefits, and how Beran can assist with advanced solutions and training.
What is condition monitoring?
Condition monitoring is a process of monitoring conditions in rotating machinery, such as vibration, to efficiently identify changes that could indicate a fault. This process is part of a predictive maintenance approach, enabling maintenance to be scheduled and preventative measures to be implemented, thus preventing asset failure or unplanned downtime.
Condition monitoring equipment allows for predictive machine maintenance. Both hardware and software can provide 24/7 measurements and data, allowing teams full visibility of their critical asset health and performance. Beran's PlantProtech™ platform offers continuous online vibration monitoring, detecting early changes in plant health and empowering operators with insightful analysis tools.
Condition monitoring is used for a range of equipment, including rotating machinery, pumps, and other assets. Sensors can measure parameters in real time and send alerts when a change is detected.
How does it work?
Ongoing real-time condition monitoring allows engineers to schedule planned maintenance rather than on a fixed date. Maintenance can be planned as required, reducing downtime. Predictive maintenance is a significant improvement over reactive maintenance, where machines are run until failure and then replaced. This approach creates higher efficiencies and avoids unexpected downtimes and costs.
What is online condition monitoring?
Online condition monitoring continuously monitors a machine. These systems can work remotely, allowing your engineers or an external specialist to perform data retrieval and analysis remotely.
Online systems can send warnings when pre-set limits are exceeded. These troubleshooting measures often occur at lower limits than those of fixed condition monitoring systems, enabling quicker and more efficient responses to wear and tear and potential maintenance needs.
Benefits of condition monitoring
- Reduces unnecessary maintenance costs: Protects assets.
- More efficient maintenance: Schedules maintenance only when necessary.
- Avoids unplanned downtime: Prevents unexpected failures.
- Provides 'always-on' monitoring: Continuous asset monitoring.
- Improved asset efficiencies: Enhances overall performance.
- Identifies potential problems faster: Early detection of issues.
- Flexible monitoring: On-site or remote options.
- Improves safety: Ensures safer operation of machinery.
How Beran can help
PlantProtech™ protection and condition monitoring systems
Our PlantProtech™ line offers comprehensive condition monitoring solutions for the power industry. This includes advanced hardware and software designed to keep your assets running smoothly.
PlantProtech™ Protor Mobile
The PlantProtech™ rotor mobile is a portable condition-monitoring machine, ideal for flexible and efficient monitoring in various environments.
On-site transducer calibration and signal loop testing
Offered UK only.
Vibration analysis and training
We specialise in vibration analysis, a crucial aspect of condition monitoring, and offer comprehensive training courses to equip your team with the necessary skills. Our upcoming course, Introduction to Rotating Machinery Vibration Diagnostics, will be held from 12-14 November 2024 in Torrington, Devon, UK.
This three-day training, led by industry experts Craig Hill and Omoruyi Onobhamiukor, is tailored for system engineers, mechanical engineers, and operations staff, including new hires and trainees. Attendees will gain essential skills in vibration monitoring and diagnosis, learn to interpret vibration data effectively and utilise historical data for predictive analysis. The course includes a certificate of attendance, a rotor dynamics manual, refreshments, and a full factory tour.
Don't miss this opportunity to enhance your diagnostic skills and optimise plant operations. Register today!
In summary
Condition monitoring ensures the safe operation of critical plant assets and improves efficiency. It allows for planned maintenance and helps eliminate unnecessary processes, saving time and money.
Talk to us about your condition monitoring requirements
Our condition monitoring specialists are on hand to ensure you get the right product for your needs.
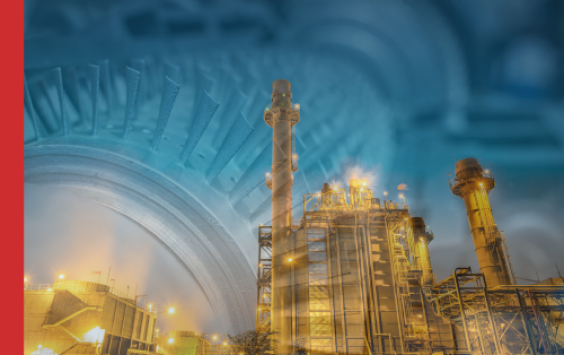
- Date: 25-26 September 2024
- Venue: Chatsworth House, Bakewell, Derbyshire, DE45 1PP
- Event organiser: Beran
Join us at the premier event for condition monitoring professionals. Connect with industry leaders, explore advancements in vibration monitoring, and discover innovative solutions to enhance operational efficiency and reliability.
Engage in expert-led sessions, hands-on demonstrations, and valuable networking opportunities.

- Date: 12 - 14 Novemberber 2024
- Venue: Torrington, Devon
- Event organiser: Beran
Enhance your skills in vibration analysis with our comprehensive three-day training course. Led by industry experts Craig Hill and Omoruyi Onobhamiukor, this training is ideal for system engineers, mechanical engineers, and operations staff. Gain essential vibration monitoring and diagnosis skills, learn to interpret vibration data, and utilise historical data for predictive analysis.