
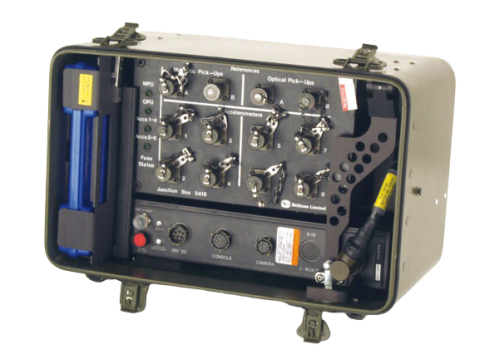
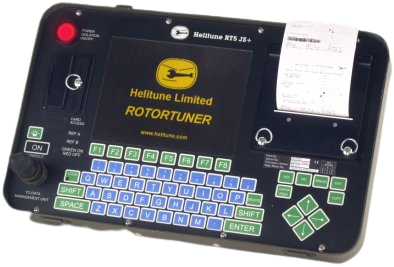



Rotortuner RT-5JS+
The Rotortuner 5JS+ is the successor to the world-famous Rotortuner Dash 5 system.
Description
The Rotortuner 5JS+ utilises the latest in DSP technology the RT-5JS+ reduces airborne test time to a minimum. Designed for reliability and with the ability to operate in the most extreme environments the RT-5JS+ provides the operator with a cost-effective upgrade or new purchase option.
Benefits
For customers looking to upgrade their obsolete Rotortuner Dash 5, the significant reductions of up to 60% in-flight test time provide a quick return on investment. The reduction in both size and weight of the Data Management Unit electronics now permits the stowage and use of the Junction Box within the original case if required. There is also space for the stowage of the transducer case for the safe storage of accelerometers, OPU, and MPU.
Operator console
The console is housed in a ruggedised container that acts as the lid for the DMU stowage container. It is equipped with a fast, high-resolution, compact printer, and a highly reliable Compact Flash card reader. The large screen size and optimised resolution provide increased clarity for the operator. When combined with the ergonomically designed hard-wearing tactile keyboard the console package provides a user-friendly interface that is easy to operate even in extreme operating conditions.
Functionality
The very latest processors provide highly superior data processing capability and true parallel harmonic acquisition. This keeps data collection times to a minimum reducing flight times significantly. An advanced FFT data collection and analysis mode is available providing high-resolution targeted FFTs configurable by the operator for in-depth diagnosis.
Operational
Combined with the new Helitune transducer cables and the Mk2 Line Scan Camera, the entire RT-5JS+ system is EMC compliant with Mil Stan 461E and UK Def. Stan. 59-41 (“above decks” compliant). The RT- 5JS+ also has an extended operating temperature range from -25ºC to +55ºC.
Compatibility
All transducers and transducer cables previously used with the older Rotortuner Dash 5 system are compatible with the RT-5JS+ (EMC compliance could be compromised with older cables). Similarly, the operating system menu structure is retained, thus minimising changes to training schedules. With industry-leading true blade tip track technology, the RT-5JS+ provides a low-risk, simple, and cost-effective upgrade option to maintain the Rotortuner as a user-friendly, efficient, and accurate RTB and vibration monitoring platform. The RT-5JS+ easily achieves current EMC standards, ensuring compatibility with new and future advanced aircraft systems, whilst still providing significant steps forward by utilising the latest technology. The RT-5JS+ is a demonstration of Helitune’s commitment to current and future customers.
Product Specification
DMU Performance Data | |
Vibration Analysis Method | Fast Fourier Transform (FFT) Analysis (Synchronous and Asynchronous) |
FFT Sizes | 1024, 2048 or 4096 Points |
FFT Line Count | 400, 800 or 1600 Lines |
Frequency Range | 0-25 R and 0-25 T (where R and T are the Main Rotor and Tail Rotor fundamental rotational speeds) and asynchronous to 10kHz with user-selectable specific frequency bands for in-depth diagnostics. |
Console display | |
Type | Electro-luminescent |
Resolution | 640x480 Pixels |
Console Test Card Interface | |
Type | Compact Flash |
MK2 Line Scan Camera | |
Aperture Range | F1.4 to F360 |
Tracking Accuracy | height +/- 2.0 mm (at tip) |
Electrical | |
DC Input | 24 – 28V at 5A maximum |
Low Voltage Directive | Mil 704C for 28V DC Operation IEC1010-1 ’Safety Requirements for Electrical Equipment for Measurement, Control and Laboratory Use‘ |
Physical data | ||
Equipment | Dimensions (mm) | Weight (kg) |
DMU | 310 x 165 x 65 | 2.00 Approx. |
Operators Console | 410 x 280 x 90 | 3.50 Approx. |
Accessories Case (empty) | 545 x 365 x 215 | 5.50 |
Line Scan Camera | 250 x 110 x 75 | 1.30 |
AC Adapter | 200 x 95 x 70 | 1.00 |
Junction Box (5418) | 260 x 160 x 90 | 1.60 |
Accelerometers | 45 x 21 dia | 0.048 |
Magnetic Reference Pick-Ups | 56 x 17 dia | 0.066 |
Optical Reference Pick-Ups | 60 x 50 x 16 | 0.050 |
Related content
The minimum Flight Routine algorithm optimises RTB maintenance time.
The Minimum Flight Routine (MFR) algorithm was introduced in 2010, to reduce the number of flights needed to perform RTB, therefore reducing operating costs and increasing aircraft availability.